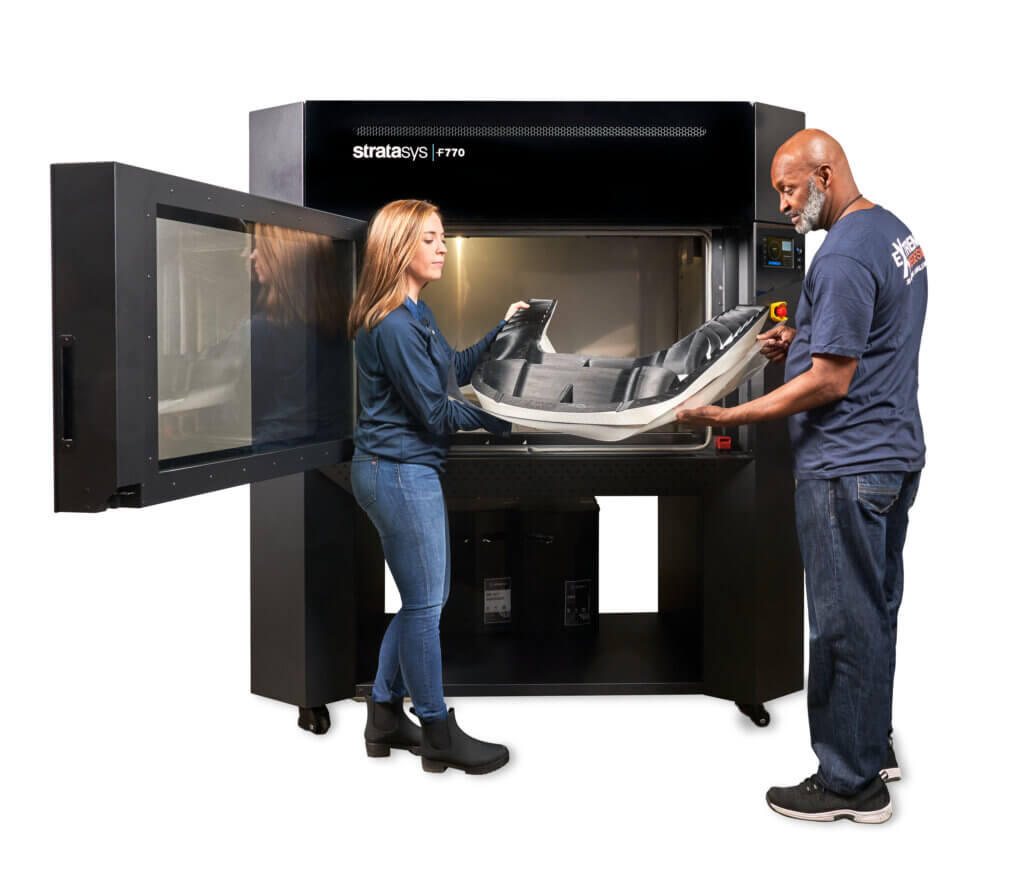
This year’s return of TCT 3Sixty at the NEC sees Laser Lines, the UK’s most established reseller of 3D printers and materials, with several stands at the exhibition. Across the…
This year’s return of TCT 3Sixty at the NEC sees Laser Lines, the UK’s most established reseller of 3D printers and materials, with several stands at the exhibition. Across the…
It’s no secret that 3D printer technology has rapidly evolved and improved over the last decade but in unprecedented times, the major advances have allowed 3D printers to play a…
After more than 45 years in the business, Laser Lines is still challenging industry norms and being the best in class. This time it’s not the products but the people….
Motor sports and 3D printing are a match made in heaven. Teams from all over the world are turning to additive manufacturing to realise cost and time savings. Using the…
Laser Lines, the UK’s most established reseller of 3D printers and materials, will be showcasing a full range of 3D printing solutions on stand D60 at TCT Show 2019. Products…
Laser Lines, a total solutions provider of 3D printers and laser equipment, today announces that it has become a UK reseller of Xact Metal’s 3D printing systems, which offer powerful…
Laser Lines has long supported medical teams, selling multi-material printers like the Stratasys J750 and Connex3range for on-site production of anatomical models. Used in pre-surgical planning, they allow consultants to plan more effective and…
Laser Lines is proud to announce it is selling and supporting a new suite of materials for its FDM and Polyjet range of printers including TPU 92A, Agilus White, Vero…
At the opening of TCT 2018 Exhibition & Conference on 3D Printing held at the NEC in Birmingham (from September 25th – 27th), Additive Industries has announced a partnership with Laser Lines…