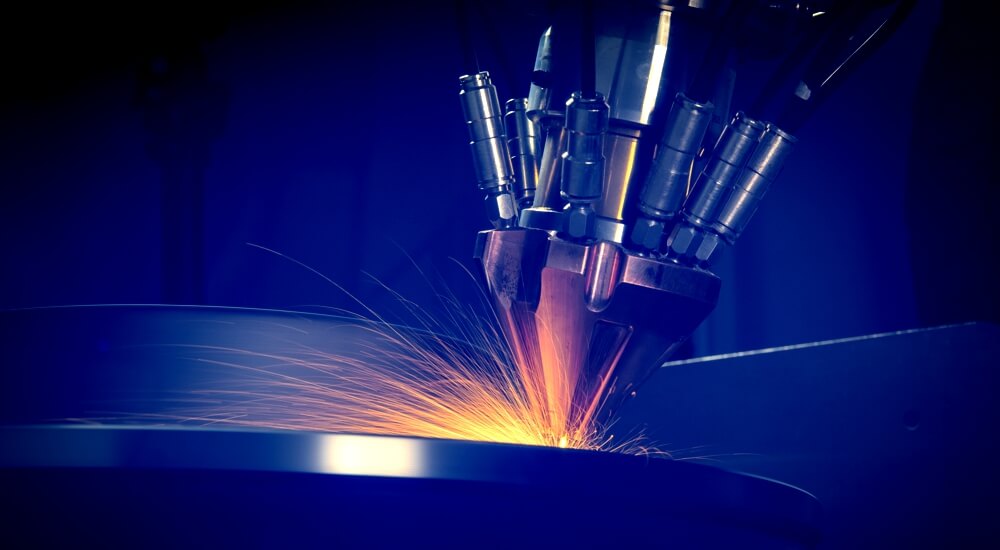
Laser Lines has PPMA on its radar where it will be exhibiting at stand A40 and showcasing its expertise in laser technology from the 24th to the 26th of September…
Laser Lines has PPMA on its radar where it will be exhibiting at stand A40 and showcasing its expertise in laser technology from the 24th to the 26th of September…
Our range of laser markers has just received an upgrade, with a new series of machines that make laser marking faster and more accurate than ever. These new machines from…
For over 30 years Industrial laser systems have been commonplace in manufacturing and R&D facilities all over the world, providing clean and efficient ways of improving manufacturing processes. Such applications…
In the context of intensified climate and environmental protection efforts, the reduction of particulate matter pollution plays an important role alongside the reduction of CO2 emissions. A relevant share of…
Established over 75 years ago, TWI is a not-for-profit research and technology organisation that provides advanced contract research and development solutions to its 700+ members. TWI’s mission is to help…
As anyone who watched Clarkson’s Farm knows, farming is a costly business, and the profits can be slim. If Britain’s farmers are to thrive at a time of shrinking subsidies…
Photonics Industries’ (PI) has announced the release of their newly updated water-cooled DX Series Q-switched UV and Green Lasers. The DX Series 355nm UV Lasers delivers the shortest Short Pulses…
What do you need to consider when selecting the best CO2 laser for your application? Lauren Knollmeyer, Synrad’s Market Analyst, goes through the important aspects including laser performance specifications, cooling methods,…
Laserline has optimized its portfolio in the high-power blue diode laser segment. In doing so, the company is making important advances in focusing properties. This is because with output powers…
Headquartered in Northamptonshire and employing 12 staff, CTR Future has been distributing laser machines in the UK since 2004, and moved into UK manufacture of British-designed laser cutting systems and engraving…